From Maintenance to Modernization: Hitachi's Comprehensive Approach to Equipment Care
- by R62
- 0
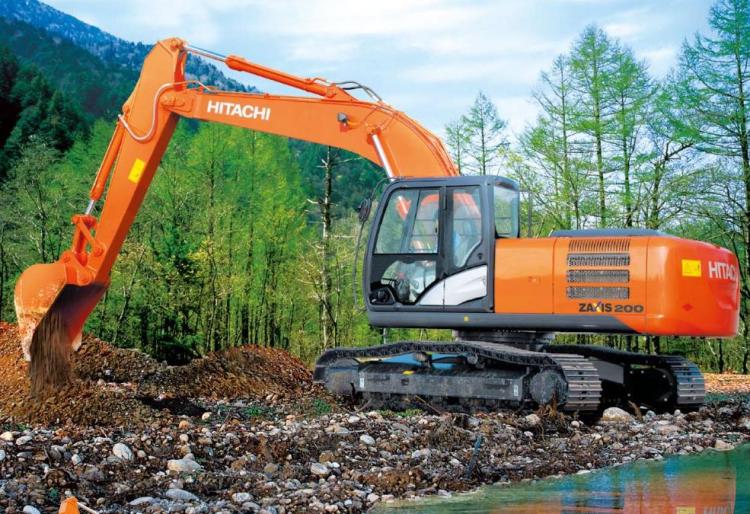
TECHNO.RMOLSUMSEL.ID - Hitachi Construction Machinery stands at the forefront of providing innovative solutions for both construction and mining industries. A testament to its commitment, the company continuously enhances the efficiency and reliability of its machinery by leveraging advanced technologies such as the Global e-Service and ConSite. These systems offer real-time monitoring and maintenance capabilities, effectively reducing downtime and boosting overall productivity.
The Global e-Service serves as a comprehensive monitoring system, keeping track of vehicle status in real-time. By utilizing advanced sensors and data analytics, it can detect potential issues before they escalate, enabling predictive maintenance and proactive troubleshooting. This proactive approach ensures optimal performance and minimizes disruptions in operations.
Another cornerstone of Hitachi's maintenance strategy is the ConSite system. Providing customers with detailed reports on equipment performance and condition, ConSite empowers informed decision-making regarding maintenance and repairs. With features like alarm reporting and failure diagnosis, it aids in early detection and resolution of potential issues, preventing major breakdowns.
Moreover, Hitachi Construction Machinery integrates advanced technologies like GPS and automation to further enhance equipment safety and efficiency. For instance, the ZAXIS-6 Series excavators feature advanced GPS guidance systems, improving accuracy and mitigating the risk of accidents.
In addition to technological advancements, Hitachi prioritizes customer satisfaction through comprehensive after-sales services. From parts and fluid supply to training and maintenance support, the company ensures that customers receive the necessary assistance to keep their equipment running at peak performance.
In summary, Hitachi Construction Machinery remains a leader in the construction and mining sectors, renowned for its dedication to innovation, quality, and customer-centric solutions. Its adoption of advanced technologies and commitment to superior customer support solidify its position as the preferred choice for industry professionals worldwide.
Strategies for Extending the Lifespan of Construction Equipment
Extending the lifespan of construction equipment is pivotal for cost reduction and enhanced productivity within the construction industry. Here are some effective strategies to achieve this objective:
-
Regular Maintenance: Consistent maintenance routines, including checks, cleaning, and lubrication, coupled with timely component replacements, are essential for prolonging equipment lifespan.
-
Proper Storage: Shielding equipment from environmental factors by storing it in dry, well-ventilated areas with protective covers prevents damage from extreme temperatures and moisture.
-
Proper Operation: Adhering to manufacturer guidelines, avoiding overloading, using correct fuel, and following recommended operating procedures prevent unnecessary wear and tear.
-
Monitoring and Tracking: Tracking equipment performance metrics, fuel consumption, and maintenance records enables timely identification and resolution of potential issues.
-
Upgrades and Modernization: Integrating new technologies and features through equipment upgrades enhances efficiency, reduces maintenance needs, and improves overall performance.
-
Training and Education: Providing comprehensive training to operators and maintenance personnel ensures proper equipment usage and maintenance, thereby extending its lifespan.
-
Parts Replacement: Timely replacement of worn-out or damaged parts prevents further deterioration, optimizing equipment performance and longevity.
-
Inspections and Audits: Conducting regular inspections and audits aids in identifying potential issues early on, averting costly breakdowns and downtime.
-
Fuel Management: Implementing proper fuel management practices, including using the correct fuel and preventing contamination, preserves equipment integrity and performance.
-
Collaboration with Manufacturers: Seeking guidance from equipment manufacturers on maintenance, operation, and upgrades facilitates effective equipment management and lifespan extension.
By implementing these strategies, construction equipment owners and operators can effectively prolong equipment lifespan, reduce costs, and enhance overall productivity.
Leveraging Technology to Enhance Construction Equipment Maintenance
Technology plays a pivotal role in revolutionizing construction equipment maintenance, offering predictive insights, real-time monitoring, and data-driven decision-making. Here's how technology can be harnessed to improve maintenance practices:
-
Predictive Maintenance: Machine learning algorithms analyze equipment data to forecast potential issues, allowing for proactive maintenance and minimizing downtime.
-
Condition-Based Maintenance: Real-time equipment data enables maintenance scheduling based on actual condition, optimizing maintenance frequency and reducing costs.
-
Asset Tracking: Technology facilitates equipment tracking and maintenance scheduling, identifying usage patterns and optimizing maintenance routines.
-
Data Analytics: Analyzing equipment data enables informed decision-making regarding maintenance scheduling, resource allocation, and performance optimization.
-
Remote Monitoring: Real-time monitoring systems provide insights into equipment performance, facilitating timely intervention and preventive maintenance.
-
Automated Reporting: Automated reporting systems offer detailed performance insights and alerts, enabling proactive maintenance and streamlined operations.
-
Collaboration and Knowledge Sharing: Technology fosters collaboration among maintenance personnel, facilitating knowledge sharing and best practice dissemination.
-
Training and Education: Technology-based training programs equip maintenance personnel with the skills needed to effectively utilize maintenance technologies and techniques.
-
Integration with Other Systems: Integration with enterprise systems enhances data exchange and facilitates seamless maintenance planning and execution.
-
Continuous Improvement: Real-time data insights drive continuous improvement efforts, refining maintenance strategies and optimizing equipment performance over time.
By leveraging these technological advancements, construction companies can enhance equipment maintenance practices, minimize downtime, and optimize resource utilization.
Challenges in Implementing Predictive Maintenance for Construction Equipment
Implementing predictive maintenance for construction equipment presents several challenges that companies must navigate effectively:
-
Data Quality and Availability: Ensuring data quality and availability from various sources, including sensors and maintenance records, is crucial for accurate predictive maintenance.
-
Skilled Personnel and Training: Analyzing complex data and deriving predictive insights necessitate skilled personnel and comprehensive training programs.
-
Implementation Complexity: Integrating predictive maintenance into existing processes and systems requires careful planning, coordination, and investment.
-
Data Security: Protecting sensitive data and ensuring system security against cyber threats are paramount considerations in predictive maintenance implementation.
-
Building Analytical Capabilities: Establishing a proficient team of data analysts with the requisite skills and expertise is essential for effective predictive maintenance.
-
Cost and ROI Justification: Demonstrating clear return on investment and justifying the costs associated with predictive maintenance implementation are critical for stakeholder buy-in.
-
Integration Challenges: Integrating predictive maintenance systems with existing enterprise systems can be complex and require significant IT resources.
-
Change Management: Overcoming resistance to change and effectively transitioning to predictive maintenance requires effective change management strategies.
-
Scalability: Ensuring predictive maintenance systems can scale with business growth and evolving needs is essential for long-term viability.
-
Regulatory Compliance: Adhering to regulatory requirements and standards, particularly concerning data privacy and security, is imperative in predictive maintenance implementation.
Addressing these challenges proactively enables construction companies to effectively implement predictive maintenance, unlock operational efficiencies, and optimize equipment performance.

FOR CODE, "PESS F5 / CLICK BUTTON REFRESH !"
Previous Article